Injection moulding and metal-plastic conversion
This gripper-head for bottling line was originally realized in stainless steel.
With the support of Csplast and thanks to the injection moulding technology it has been possible an optimal re-design of the object from metal to plastic.
The metal–plastic conversion with the injection moulding technique represent an innovative choice with several benefits:
• Use of a material with an extremely hight elastic module, which is comparable with a lot of die casting alloys also at high working temperature;
• Resistance to chemical agents, which are often used for washing and disinfection;
• The respect of precise dimensional tolerances, thanks to the right combination of injection molding technology and the choice of the most appropriate molding material. This means that the product is immediately usable without having to resort to post-molding CNC machining;
• Weight reduced by 81%;
• Production cost reduced by more than 70% compared to the metal construction.
The injection moulding is the perfect solution for plastic objects mass production. With the realization of multi cavities moulds we produce pieces equal to each other at the same time. Moreover, this technology reduces the production time and the costs.
To realize this kind of production we use granules of plastic, which will be melted and injected at high pressure in the steel moulds with injection moulding machine. After this phase the melted polymer cools down and solidifies with the desired form.
#Designformanufacturing #Letsdesignfuture
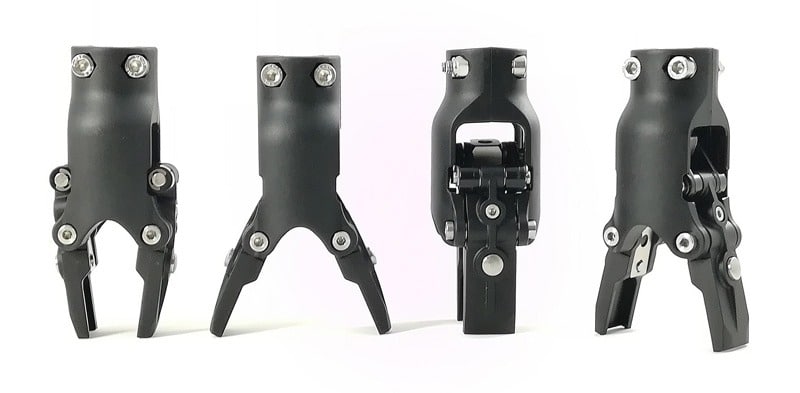